-
- EXPLORAR
-
-
-
-
-
-
-
Future-Proofing Oil & Gas with High-Performance Composites
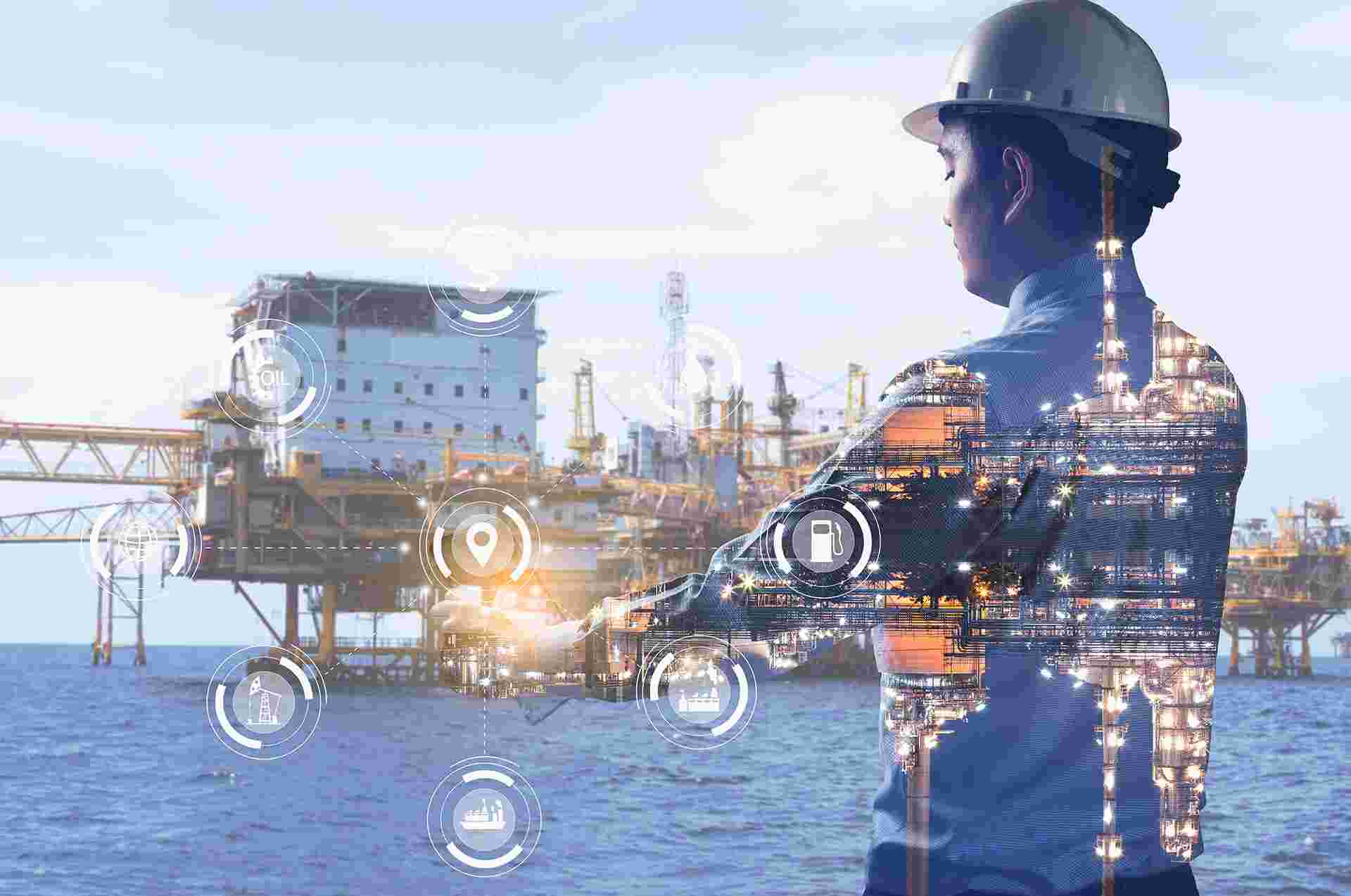
The oil and gas industry, traditionally reliant on metals like steel and aluminum, is increasingly turning to composite materials. These advanced materials are gaining traction across upstream, midstream, and downstream sectors, driven by their superior performance in harsh environments. From subsea pipelines to offshore platforms, composites are proving their value in enhancing operational efficiency, safety, and sustainability. The composites in oil & gas industry market is projected to grow from USD 2.3 billion in 2022 to USD 3.4 billion by 2028, at a CAGR of 6.1% during the forecast period. There is an increased requriemnet of durable and cost efficie composites component solutions for oil & gas industry. Composites offer several benefits over traditional materials such as steel, including greater durability, corrosion resistance, and weight reduction.
Applications of Composites in Oil & Gas Composites are used in a wide range of applications in the oil and gas sector. Common uses include pipes, risers, tanks, pressure vessels, downhole tubing, and umbilicals. These materials are especially valuable in challenging environments such as offshore platforms and onshore drilling sites where durability, corrosion resistance, and strength are critical.
Download PDF Brochure: https://www.marketsandmarkets.com/pdfdownloadNew.asp?id=75947166
Comparing Composites with Steel Compared to steel, composites offer a higher strength-to-weight ratio, excellent corrosion resistance, and longer service life. Unlike steel, which is prone to rust and requires regular maintenance, composites maintain integrity in corrosive environments, significantly reducing downtime and maintenance costs.
Advantages in Offshore and Pipeline Applications Composites are particularly advantageous in offshore and pipeline applications. Their resistance to saltwater corrosion, lighter weight, and superior fatigue resistance make them ideal for deepwater and ultra-deepwater projects. Additionally, their ease of installation and reduced maintenance needs translate into lower total ownership costs.
Types of Composites Used The primary types of composites used in oil and gas include:
-
Glass fiber-reinforced plastics (GFRP): Common in tanks and piping
-
Carbon fiber-reinforced plastics (CFRP): Valued for their high strength
-
Thermoplastic composites: Known for chemical resistance and recyclability
Each material type is selected based on specific application requirements, such as pressure tolerance, chemical exposure, and mechanical stress.
Challenges to Adoption Despite their benefits, composites face several barriers to widespread adoption in the oil and gas industry:
-
Higher initial material costs
-
Limited industry standards and specifications
-
Conservative industry mindset
-
Complexity in inspection and repair techniques
However, ongoing research, improved manufacturing methods, and increased familiarity are helping overcome these obstacles.
Regional Growth Drivers
-
North America: Leading the market due to shale gas developments and offshore projects
-
Middle East: Increasing use in infrastructure upgrades and non-metallic initiatives
-
Europe: Emphasis on sustainable operations and retrofitting aged infrastructure
-
Asia-Pacific: Rapid industrial growth and investments in energy infrastructure
Get a Sample Copy of This Report: https://www.marketsandmarkets.com/requestsampleNew.asp?id=75947166
Key Market Players Prominent companies in the composites market for oil and gas include:
-
National Oilwell Varco (NOV)
-
TechnipFMC
-
Schlumberger
-
Baker Hughes
-
Owens Corning
-
Hexcel Corporation
-
Hengrun Group
These companies are investing in advanced composite solutions for risers, pipelines, tanks, and structural applications.
Strohm is a Netherlands-based technology company that specializes in the design and manufacture of thermoplastic composite pipes for use in the oil & gas industry. Airborne International was founded by 2 aerospace engineers in 1995 in The Netherlands. In October 2020, Airborne Oil & Gas rebranded to Strohm. The company majorly operates in two business segment, namely, renewable energy and oil & gas. The company develops, manufactures, and distributes fully bonded thermoplastic composite pipes composed of glass or carbon fiber reinforcements to the offshore oil & gas industry. It provides a wide range of oil & gas thermoplastic composite pipes such as flowline, jumper, and riser. The company manufactures flowlines, and risers for production applications, and jumpers for intervention applications. These thermoplastic composite pipes provide unique properties such as corrosion, fatigue, and chemical resistance; lightweight; flexibility, which makes it superior to be used in the offshore oil & gas industry. Strohm has its production facilities in IJmuiden, Netherlands and Seaport IJmuiden/Amsterdam. The company has qualified design methods and production process for Thermoplastic Composite Pipes (TCP) in accordance with the new DNV standard, DNVGL RP F119. The company mainly operates in Asia Pacific, Europe, North America, Middle East & Africa and Latin America. In January 2023, Strohm secured a second contract from ExxonMobil to supply more than 24 jumpers for the development of the Uaru field situated offshore Guyana, in the Americas.
NOV Inc. (US)
NOV Inc. is a leading global provider of equipment and technology to the oil & gas industry. The company was founded in 1841 and is headquartered in Houston, Texas, US. NOV's operations are divided into three business segments: Wellbore Technologies, Completion & Production Solutions, and rig Technologies. It offers its composite pipe products through the Completion & Production Solutions business segment. The company is present in the Asia Pacific, Americas, Europe, and other regions. NOV operates in more than 60 countries and has a diverse customer base that includes oil & gas companies, drilling contractors, and other service providers. The company has a strong reputation for innovation and has a history of developing and commercializing new technologies that have helped improve efficiency and safety in the oil & gas industry. In June 2022, NOV and Aker Solutions signed a new long-term technology cooperation agreement to optimize Subsea system solutions, enabling sustainable oil & gas operations.
Speak to Expert: https://www.marketsandmarkets.com/speaktoanalystNew.asp?id=75947166
Utilization in the Middle East In the Middle East, composites are being increasingly used in non-metallic pipelines, modular offshore structures, and corrosion-resistant downhole components. Saudi Aramco’s Nonmetallic Initiative is a key driver in promoting composite use across upstream and downstream segments.
Corrosion Resistance in Pipelines One of the greatest benefits of composites is their resistance to internal and external corrosion. This makes them particularly suitable for pipelines transporting corrosive fluids such as sour gas, reducing the risk of failure and environmental contamination.
Thermoplastic Composites in Deepwater Drilling Thermoplastic composites are gaining popularity in deepwater applications due to their flexibility, fatigue resistance, and weldability. They are increasingly used in umbilicals, risers, and flowlines, and their recyclability makes them an environmentally friendly option.
Environmental Benefits
-
Reduced material weight decreases fuel consumption during transport
-
Lower maintenance and replacement frequency
-
Non-metallic nature minimizes risk of environmental damage from corrosion
-
Potential for recyclability and reuse
Future Outlook by 2030 The composites market in the oil and gas industry is expected to witness significant growth through 2030. Trends include increased use in offshore and subsea installations, greater acceptance of standardized materials, and growing demand from emerging economies. Integration with smart monitoring systems is also anticipated.
Innovation Trends
-
Hybrid composites combining multiple fiber types
-
3D printing for rapid prototyping
-
Smart composites with embedded sensors
-
Fire-resistant and conductive composite variants
Inquire Before Buying: https://www.marketsandmarkets.com/Enquiry_Before_BuyingNew.asp?id=75947166
Impact on Performance Composite risers and downhole tubing are improving overall system performance. Their lightweight design and resistance to wear extend operational life and enhance extraction efficiency.
Adoption in Shale and Fracking In North American shale plays, composites are used in high-pressure flowback lines, chemical storage tanks, and pump housings. Their resistance to abrasive fluids and chemicals makes them suitable for harsh fracking conditions.
Conclusion - Composites are revolutionizing the oil and gas industry by offering enhanced durability, reduced maintenance, and improved environmental performance. With ongoing technological advances and rising demand across global regions, composites are poised to become a foundational material in the future of oil and gas operations.
- Composites_in_Oil_and_Gas_Industry_Market_Size
- Composites_in_Oil_and_Gas_Industry_Market_Share
- Composites_in_Oil_and_Gas_Industry_Market_Type
- Composites_in_Oil_and_Gas_Industry_Market_Application
- Composites_in_Oil_and_Gas_Industry_Market_Region
- Composites_in_Oil_and_Gas_Industry_Market_Research
- Composites_in_Oil_and_Gas_Industry_Industry
- Whats New
- Shopping
- Wellness
- Sports
- Theater
- Religion
- Party
- Networking
- Music
- Literature
- Art
- Health
- Jogos
- Food
- Drinks
- Fitness
- Gardening
- Dance
- Causes
- Film
- Crafts
- Other/General
- Cricket
- Grooming
- Technology