Mastering Sand Casting: A Comprehensive Guide to Techniques and Benefits
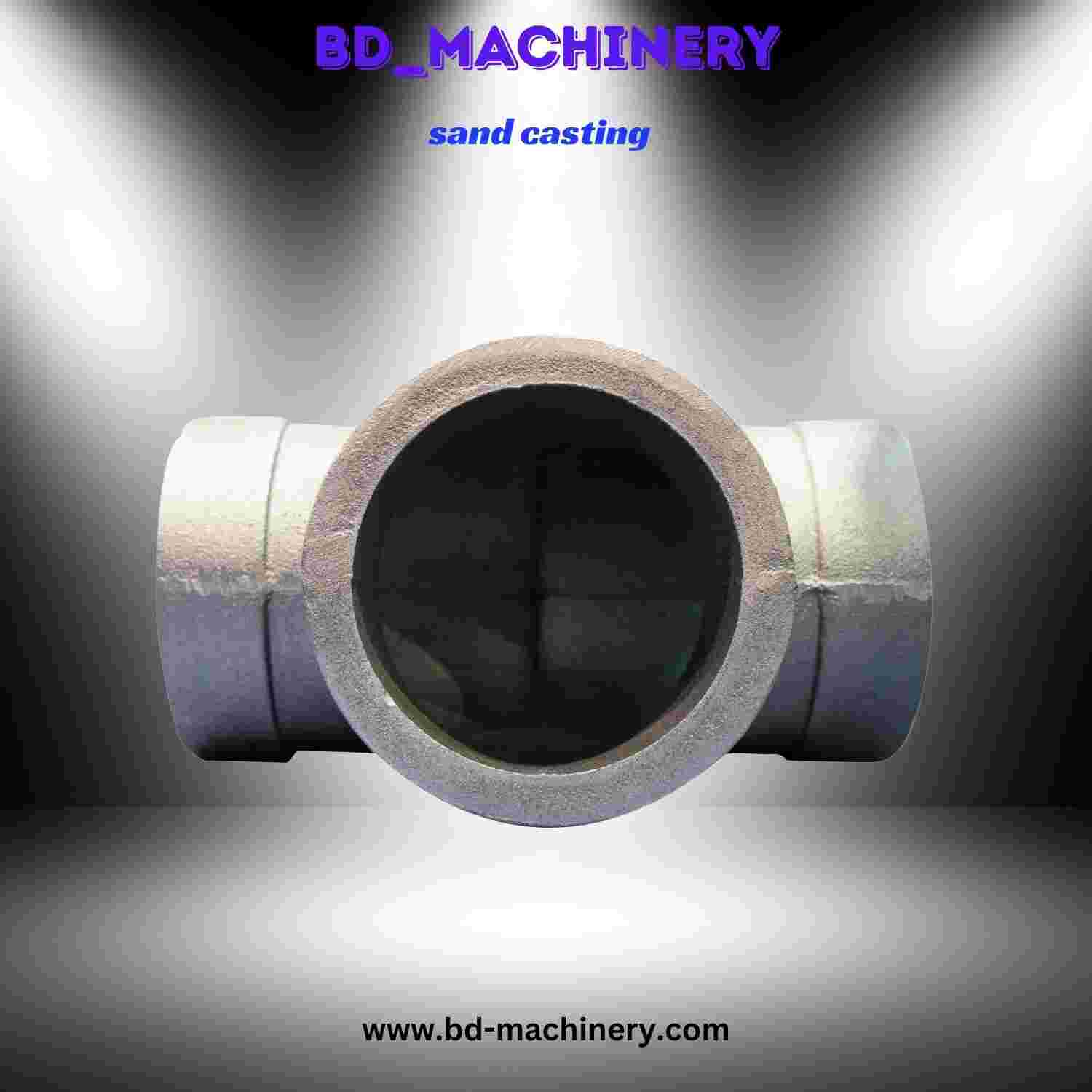
Sand casting is one of the oldest and most widely used methods for producing metal parts. This versatile and cost-effective technique allows for the creation of complex shapes and has applications in various industries, from automotive to aerospace. This guide will provide an in-depth look at sand casting, including its process, advantages, and practical tips.
-
What is Sand Casting?
- Sand casting involves creating a mold from a sand mixture and pouring molten metal into the cavity to form a desired shape.
- The process is used to cast metals such as iron, aluminum, bronze, and brass, producing a wide range of parts from engine blocks to artistic sculptures.
-
The Sand Casting Process:
- Pattern Creation: A pattern, typically made of wood, plastic, or metal, is created in the shape of the desired part. This pattern includes allowances for shrinkage and machining.
- Mold Making: The pattern is placed in a flask, and sand mixed with a bonding agent is packed around it to form the mold. The mold is divided into two halves: the cope (top) and the drag (bottom).
- Core Placement: If the part requires internal cavities or intricate internal features, cores (made from sand or other materials) are placed inside the mold.
- Pouring: The mold halves are assembled, and molten metal is poured into the mold cavity through a gating system.
- Cooling and Removal: Once the metal solidifies and cools, the mold is broken away, revealing the cast part. The part is then cleaned and finished as needed.
-
Advantages of Sand Casting:
- Versatility: Sand casting can produce parts in a wide range of sizes, from small components to large structures.
- Cost-Effective: The materials and tools required for sand casting are relatively inexpensive, making it a cost-effective manufacturing method.
- Adaptability: The process can accommodate various metals and alloys, offering flexibility in material selection.
- Complex Geometries: Sand casting is capable of producing complex shapes and intricate details that may be challenging for other casting methods.
-
Practical Tips for Sand Casting:
- Pattern Design: Ensure the pattern design includes proper draft angles to facilitate easy removal from the mold without damaging the sand structure.
- Mold Quality: Use high-quality sand and bonding agents to create a strong and precise mold. Properly pack and compact the sand to avoid defects.
- Temperature Control: Maintain the appropriate temperature for the molten metal to ensure complete filling of the mold and reduce the risk of defects such as porosity or cold shuts.
- Ventilation: Incorporate vents in the mold to allow gases to escape during pouring, preventing gas-related defects in the cast part.
- Post-Casting Treatment: After removing the cast part from the mold, perform necessary post-casting treatments such as heat treatment, machining, and surface finishing to achieve the desired properties and dimensions.
Conclusion: Sand casting is a robust and adaptable manufacturing process that offers numerous benefits for producing metal parts with complex geometries. By understanding the sand casting process and applying best practices, manufacturers can achieve high-quality results and leverage the full potential of this traditional yet enduring technique.
- Whats New
- Shopping
- Wellness
- Sports
- Theater
- Religion
- Party
- Networking
- Music
- Literature
- Art
- Health
- Games
- Food
- Drinks
- Fitness
- Gardening
- Dance
- Causes
- Film
- Crafts
- Other/General
- Cricket
- Grooming
- Technology