Precision Matters: The Science Behind Set Screw Performance
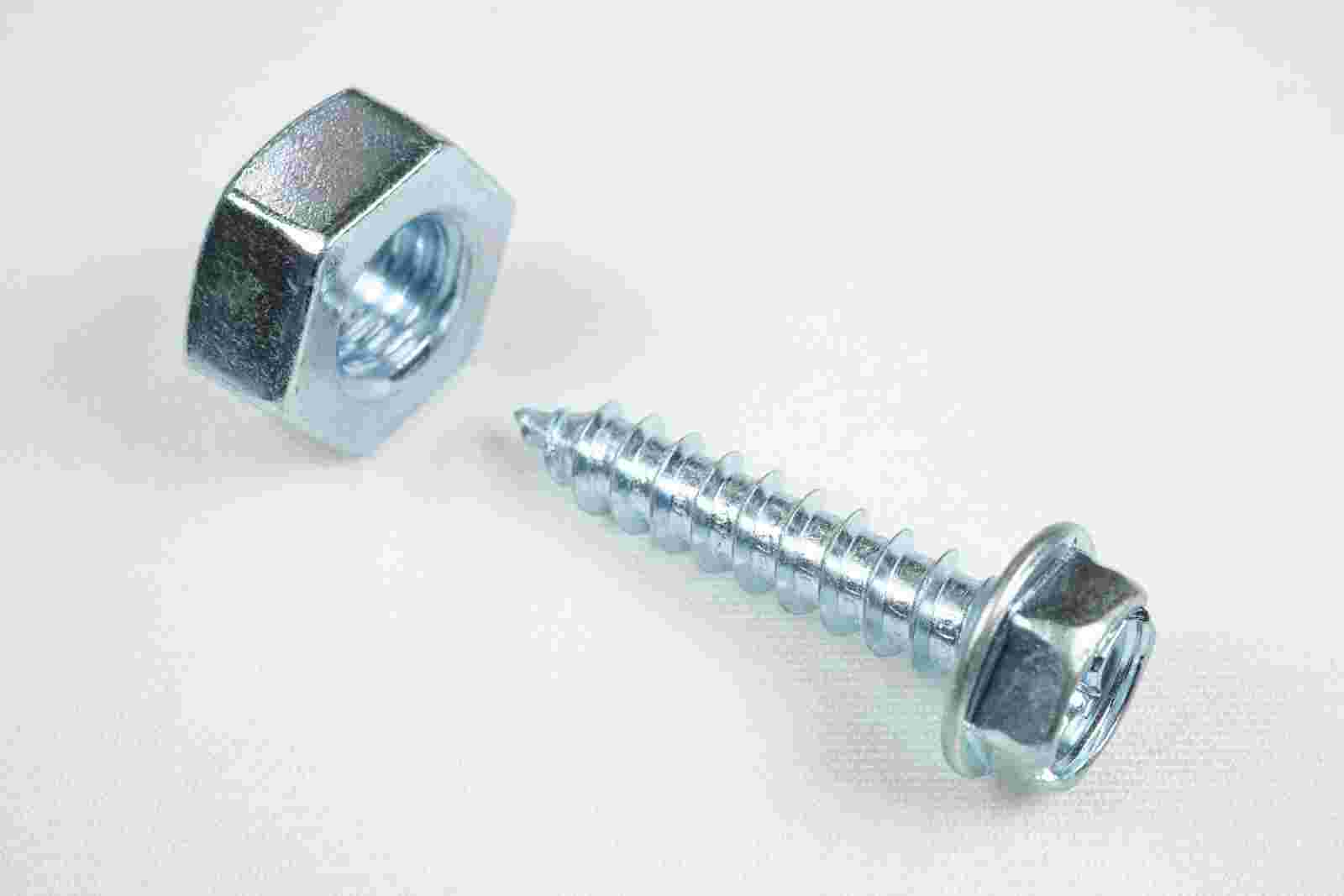
Set screws may seem like small components in the vast machinery of modern engineering, but their significance cannot be overstated. These seemingly simple devices play a crucial role in securely fastening two or more components together, ensuring stability, alignment, and efficiency in various mechanical systems. However, their effectiveness hinges greatly on precision – from design to material selection and manufacturing processes. In this article, we delve into the science behind set screw performance, highlighting why precision matters in their design and application.
Understanding Set Screws:
Before delving into the intricacies of set screw performance, it's essential to understand what they are and how they work. Set screws, also known as grub screws or blind screws, are threaded fasteners designed to secure an object within or against another object, typically by exerting pressure through the screw's tip against the object's surface. Unlike traditional screws, which are meant to penetrate and join materials, set screws are primarily used for non-permanent fastening, often in situations where adjustment or disassembly is required.
Key Factors Affecting Performance:
Several factors influence the performance of set screws, ranging from material properties to thread design and installation torque. Let's explore some of the critical elements:
1. Material Selection: The choice of material greatly impacts a set screw's performance. Common materials include stainless steel, alloy steel, and brass, each offering different levels of strength, corrosion resistance, and durability. Selecting the appropriate material based on environmental conditions, load requirements, and other factors is crucial for optimal performance.
2. Thread Design: The thread geometry of a set screw plays a significant role in its gripping ability and resistance to loosening. Fine threads provide greater holding power but may be more susceptible to damage, while coarse threads offer better resistance to vibration. Additionally, thread-locking features such as patches or nylon inserts can enhance stability and prevent loosening under operational stresses.
3. Surface Finish: The surface finish of a set screw affects its frictional properties and ability to grip the mating surface. A smoother surface finish typically reduces friction, making installation easier but may compromise holding power. Conversely, a rougher surface finish enhances grip but may require higher installation torque.
4. Installation Torque: Proper installation torque is critical for ensuring optimal performance and preventing over-tightening, which can lead to thread stripping or deformation. Insufficient torque, on the other hand, may result in inadequate clamping force, leading to loosening under operational loads.
The Role of Precision:
Precision is paramount in every aspect of set screw design, manufacturing, and application. Even minor deviations in dimensions, tolerances, or surface finish can significantly impact performance and reliability. Here's why precision matters:
1. Consistent Engagement: Precisely machined threads ensure uniform contact between the set screw and mating surface, maximizing gripping force and minimizing the risk of slippage or loosening.
2. Optimal Material Properties: Accurate material composition and heat treatment processes are essential for achieving the desired mechanical properties, such as strength, hardness, and corrosion resistance, ensuring long-term reliability in diverse operating conditions.
3. Reliable Thread Locking: Precision application of thread-locking features, such as adhesives or mechanical locking mechanisms, ensures reliable performance without compromising thread integrity or ease of disassembly.
4. Uniform Surface Finish: A uniform surface finish reduces variability in frictional forces, enabling consistent torque application during installation and enhancing the set screw's gripping ability without sacrificing ease of assembly.
5. Quality Control: Rigorous quality control measures throughout the manufacturing process are essential for detecting and correcting any deviations from design specifications, ensuring that each set screw meets the required standards for performance and reliability.
Conclusion:
Set screws may be small in size, but their impact on the performance and reliability of mechanical systems cannot be understated. Precision in design, manufacturing, and application is crucial for maximizing their effectiveness and ensuring optimal performance under varying operating conditions. By understanding the science behind set screw performance and prioritizing precision at every stage, engineers and manufacturers can enhance the stability, alignment, and efficiency of mechanical assemblies, contributing to the overall success of diverse engineering endeavors.
- Whats New
- Shopping
- Wellness
- Sports
- Theater
- Religion
- Party
- Networking
- Music
- Literature
- Art
- Health
- Giochi
- Food
- Drinks
- Fitness
- Gardening
- Dance
- Causes
- Film
- Crafts
- Other/General
- Cricket
- Grooming
- Technology