From Blueprint to Reality: Mechatron's Mechanical Design Process Demystified
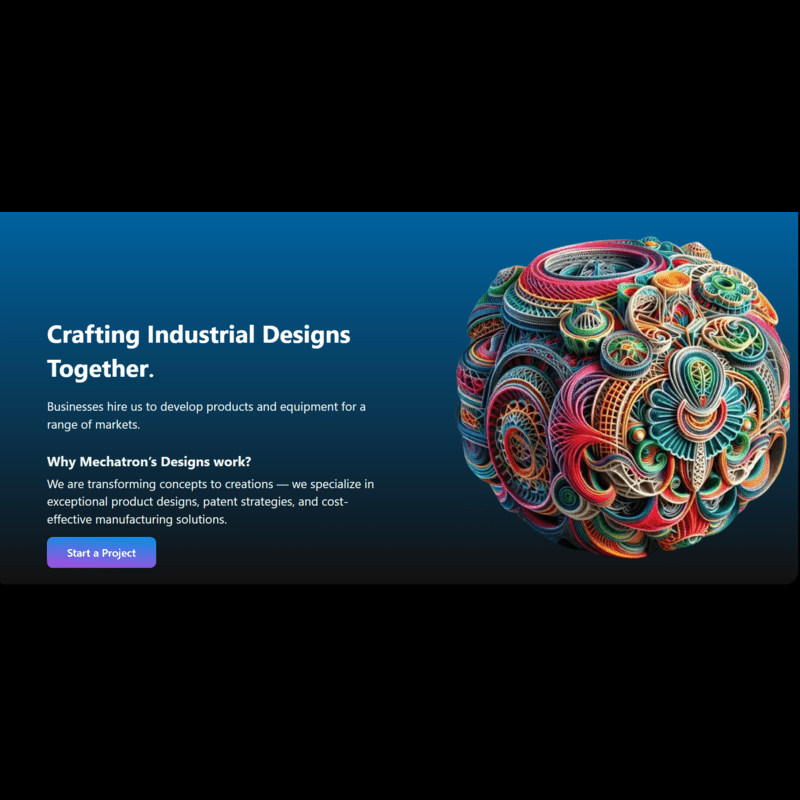
Mechatronics, an interdisciplinary field combining mechanical engineering, electrical engineering, computer science, and control engineering, has revolutionized various industries with innovative solutions. At the heart of any mechatronic system lies its mechanical design, a meticulous process that transforms abstract concepts into tangible reality. In this comprehensive guide, we delve into the intricacies of Mechatron's Mechanical Design Process, uncovering the journey from blueprint to reality.
Introduction to Mechatron's Mechanical Design Process
Mechatronics, a portmanteau of "mechanical" and "electronics," encompasses the integration of mechanical components with electronic and computer-controlled systems. Its mechanical design process forms the backbone of creating efficient and reliable mechatronic systems.
Comprehensive Overview of Mechatron's Site: Mechanical Design Services
Mechanical design services are an integral component of comprehensive mechanical engineering services, offering specialized expertise in the conceptualization, development, and optimization of mechanical systems and components. These services encompass a wide range of activities, including conceptual design, detailed engineering, and prototyping, aimed at delivering innovative and efficient solutions to meet client requirements. With a strong focus on precision, reliability, and cost-effectiveness, mechanical design services leverage advanced technologies and methodologies to transform conceptual ideas into tangible products.
By collaborating closely with clients throughout the design process, mechanical engineers ensure that the final solutions not only meet technical specifications but also align with project objectives and constraints. Whether it's designing complex machinery, automotive components, or consumer products, mechanical design services play a pivotal role in driving innovation and competitiveness in various industries.
Understanding the Blueprint
Defining Mechatronics
Mechatronics entails the synergistic integration of mechanical, electrical, and computer systems to design and manufacture products and processes. This multidisciplinary approach enables the creation of innovative solutions that leverage the strengths of each field.
Importance of Mechanical Design in Mechatronics
Mechanical design lays the foundation for mechatronic systems, dictating their functionality, durability, and efficiency. By meticulously designing mechanical components, engineers ensure that the final product meets performance requirements and withstands operational stresses.
Preliminary Research and Conceptualization
Identifying Requirements and Constraints
Before diving into the design phase, thorough research is conducted to identify project requirements, constraints, and objectives. This involves understanding the needs of end-users, regulatory requirements, budgetary constraints, and technological limitations.
Brainstorming Ideas
Creative brainstorming sessions involve interdisciplinary teams to explore various design concepts and solutions. By fostering collaboration between mechanical engineers, electrical engineers, and software developers, innovative ideas are generated that push the boundaries of traditional design approaches.
Sketching and Prototyping
Translating Concepts into Physical Form
Initial ideas are sketched and transformed into physical prototypes to visualize and evaluate design feasibility. This iterative process allows engineers to quickly iterate on design concepts, identify potential issues, and refine their ideas before committing to detailed design work.
Iterative Prototyping Process
Prototypes undergo iterative refinement based on feedback and testing results to enhance functionality and performance. By continuously refining prototypes through iterative testing and evaluation, engineers can identify and address design flaws early in the development process, reducing the risk of costly redesigns later on.
Computer-Aided Design (CAD)
Utilizing Software Tools for Precision
CAD software enables engineers to create detailed 3D models with precision and accuracy. By leveraging CAD tools, engineers can quickly iterate on design concepts, explore different configurations, and simulate performance under various operating conditions.
Creating Detailed 3D Models
Design iterations are executed digitally, allowing for comprehensive analysis and visualization of the final product. This digital prototyping approach enables engineers to identify potential design issues, optimize performance, and streamline the manufacturing process before physical prototypes are built.
Analysis and Simulation
Stress Testing and Structural Analysis
Finite Element Analysis (FEA) tools are employed to assess structural integrity and identify potential weak points. By subjecting virtual prototypes to simulated loads and stresses, engineers can identify areas of high stress concentration, optimize material usage, and ensure that the final design meets safety and performance requirements.
Simulating Performance under Various Conditions
Dynamic simulations simulate real-world conditions to evaluate system performance and behavior. By simulating the behavior of mechatronic systems under various operating conditions, engineers can identify potential performance bottlenecks, optimize control algorithms, and ensure that the final product meets customer expectations.
Material Selection and Sourcing
Choosing Appropriate Materials
Materials are selected based on mechanical properties, environmental factors, and cost considerations. By carefully selecting materials that meet the specific requirements of the application, engineers can optimize performance, reduce manufacturing costs, and minimize environmental impact.
Considering Factors like Cost, Durability, and Availability
Material sourcing involves evaluating suppliers and ensuring the availability of components for production. By establishing relationships with reliable suppliers and optimizing the supply chain, engineers can ensure a steady supply of materials and components, minimizing production delays and cost overruns.
Manufacturing and Fabrication
Setting Up Production Processes
Manufacturing processes are established, considering factors such as volume, complexity, and cost-effectiveness. By selecting the most appropriate manufacturing processes for the specific requirements of the project, engineers can optimize production efficiency, minimize waste, and ensure consistent product quality.
CNC Machining, 3D Printing, and Assembly
Modern techniques like CNC machining and 3D printing are utilized for rapid prototyping and production. By leveraging advanced manufacturing technologies, engineers can reduce lead times, lower production costs, and produce complex geometries that are not feasible with traditional manufacturing methods.
Quality Control and Testing
Ensuring Compliance with Standards
Stringent quality control measures are implemented to meet industry standards and regulatory requirements. By establishing comprehensive quality control processes, engineers can ensure that the final product meets performance specifications, regulatory requirements, and customer expectations.
Conducting Rigorous Testing Procedures
Mechatronic systems undergo comprehensive testing to verify functionality, reliability, and safety. By subjecting prototypes to rigorous testing protocols, engineers can identify and address design flaws, validate performance specifications, and ensure that the final product meets customer requirements.
Refinement and Iteration
Addressing Issues and Improving Designs
Feedback from testing and evaluation phases is incorporated to refine and optimize designs. By soliciting feedback from end-users, stakeholders, and testing protocols, engineers can identify areas for improvement, address design flaws, and optimize performance.
Incorporating Feedback for Enhancements
Continuous improvement drives iterative design cycles, ensuring optimal performance and user satisfaction. By incorporating feedback from stakeholders and end-users, engineers can identify opportunities for enhancements, prioritize design changes, and continuously improve the product throughout its lifecycle.
Documentation and Finalization
Creating Comprehensive Documentation
Detailed documentation of design specifications, processes, and testing results is compiled for future reference. Engineers can ensure traceability, facilitate knowledge transfer, and support ongoing maintenance and troubleshooting efforts by documenting the entire design process.
Finalizing Designs for Production
Final designs are approved for production, marking the culmination of the mechanical design process. By finalizing designs for production, engineers can initiate manufacturing processes, coordinate with suppliers, and prepare for product launch and distribution.
Case Study: Application in Robotics
Examining a Real-Life Example
A case study showcases the application of Mechatron's Mechanical Design Process in developing a robotic arm. By examining a real-life example, engineers can illustrate the practical application of the design process, highlight design challenges, and demonstrate innovative solutions.
Highlighting Design Challenges and Solutions
Design challenges such as weight optimization and actuator selection are addressed through innovative solutions. By highlighting design challenges and solutions, engineers can share best practices, lessons learned, and practical insights that inform future design efforts.
Future Trends and Innovations
Emerging Technologies in Mechatronics
Advancements in artificial intelligence, additive manufacturing, and materials science pave the way for future innovations. By exploring emerging technologies, engineers can anticipate future trends, identify new opportunities, and stay at the forefront of technological advancements.
Potential Impact on Mechanical Design Processes
These technologies are poised to revolutionize mechanical design processes, enhancing efficiency and enabling new possibilities. By embracing emerging technologies, engineers can streamline design workflows, optimize performance, and unlock new capabilities that drive innovation and competitiveness.
Conclusion
In conclusion, Mechatron's Mechanical Design Process serves as a cornerstone in the development of mechatronic systems, bridging the gap between conceptualization and realization. By following a systematic approach encompassing research, prototyping, analysis, and refinement, engineers can bring innovative ideas to life, driving progress and innovation across industries.
- Whats New
- Shopping
- Wellness
- Sports
- Theater
- Religion
- Party
- Networking
- Music
- Literature
- Art
- Health
- Giochi
- Food
- Drinks
- Fitness
- Gardening
- Dance
- Causes
- Film
- Crafts
- Other/General
- Cricket
- Grooming
- Technology