Importance of Technology in Manufacturing
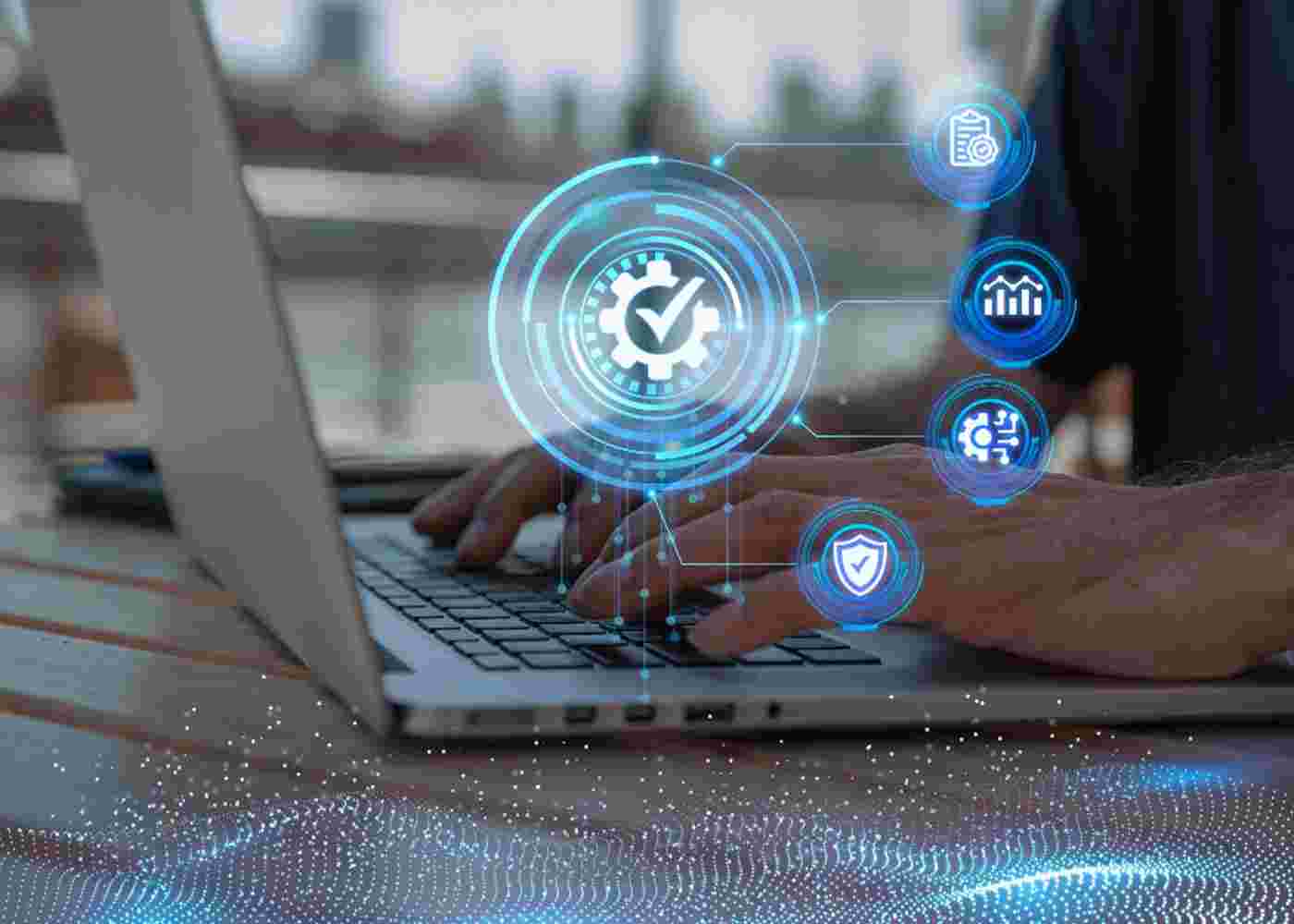
In the realm of manufacturing, technology plays a pivotal role in driving efficiency, productivity, and innovation. With the rapid advancements in automation, robotics, and artificial intelligence, manufacturers can streamline their processes, reduce costs, and enhance the quality of their products. Incorporating cutting-edge technologies into manufacturing operations not only accelerates production but also enables companies to stay competitive in the ever-evolving market landscape.
Moreover, the Hi Tech and Manufacturing Service in manufacturing enables companies to adapt to changing consumer demands, customize products on a mass scale, and minimize human error. By leveraging data analytics, IoT devices, and smart sensors, manufacturers can gain valuable insights into their production processes, identify areas for improvement, and make informed decisions to optimize their operations. Embracing technology in manufacturing is no longer a luxury but a necessity for companies looking to thrive in the digital age.
Key Technologies Driving Innovation in Manufacturing
In the fast-paced world of manufacturing, technology plays a vital role in driving innovation and transformation. One of the key technologies revolutionizing the industry is 3D printing. This cutting-edge technology allows manufacturers to create complex and customized components with precision and efficiency, reducing lead times and costs significantly.
Another important technology driving innovation in manufacturing is the Internet of Things (IoT). By connecting various devices and systems through a network, IoT enables real-time data monitoring and analysis, leading to improved efficiency, predictive maintenance, and better decision-making. This interconnected approach streamlines processes, enhances productivity, and ultimately creates a more agile and competitive manufacturing environment.
Challenges Faced by Manufacturers in Adopting High-Tech Solutions
High-tech solutions have become increasingly essential in modern manufacturing processes, offering improved efficiency, accuracy, and competitiveness. However, manufacturers often encounter significant challenges when attempting to adopt these advanced technologies. One major hurdle is the high initial investment required for implementing and integrating high-tech solutions into existing operations. Many manufacturers, particularly small and medium-sized enterprises, may struggle to allocate sufficient resources for purchasing and installing complex machinery, software, and other technological tools necessary for enhancing their production processes.
Additionally, another common challenge faced by manufacturers is the lack of in-house expertise and technical knowledge needed to effectively leverage high-tech solutions. Implementing advanced technologies often requires specialized skills and training that may not be readily available within the organization. This skills gap can hinder the successful adoption of new technologies and limit the ability of manufacturers to fully optimize their operations for improved productivity and innovation.
The Role of Artificial Intelligence in Modern Manufacturing
Artificial Intelligence is quickly becoming a game-changer in modern manufacturing processes. Its ability to analyze vast amounts of data in real-time allows manufacturers to optimize production efficiency and quality control like never before. AI algorithms can identify patterns and anomalies in the manufacturing process, enabling proactive maintenance and minimizing equipment downtime.
Furthermore, AI-powered predictive analytics enables manufacturers to forecast demand more accurately, optimize inventory levels, and enhance supply chain management. By leveraging AI in manufacturing operations, companies can make smarter decisions based on data-driven insights, streamline production processes, and ultimately improve their bottom line.
Advantages of Implementing IoT in Manufacturing Processes
IoT, or the Internet of Things, has significantly transformed manufacturing processes by enabling real-time monitoring and data collection. This technology allows manufacturers to gather valuable insights on equipment performance, production efficiency, and quality control. As a result, companies can make informed decisions to optimize operations and minimize downtime, leading to increased productivity and cost savings.
Furthermore, the implementation of IoT in manufacturing processes enhances predictive maintenance capabilities. By utilizing sensors and connectivity, organizations can proactively identify potential equipment failures before they occur. This predictive maintenance approach reduces unplanned downtime and costly repairs, ultimately improving overall equipment effectiveness and boosting business performance.
How Robotics is Revolutionizing the Manufacturing Industry
The integration of robotics in the manufacturing industry has been transforming the way products are being made. Automation through robotics enables manufacturers to achieve higher precision, consistency, and efficiency in their production processes. Robots are capable of performing repetitive tasks with speed and accuracy, which not only increases productivity but also reduces the margin of error in manufacturing operations.
Moreover, robotics in manufacturing has revolutionized the concept of smart factories, where interconnected robotic systems work collaboratively with human workers to optimize production lines. This collaboration leads to enhanced safety measures, better resource utilization, and ultimately, improved overall quality of products. As robots become more advanced and versatile, they are playing a pivotal role in pushing the boundaries of traditional manufacturing techniques and opening up new possibilities for innovation in the industry.
- Whats New
- Shopping
- Wellness
- Sports
- Theater
- Religion
- Party
- Networking
- Music
- Literature
- Art
- Health
- Games
- Food
- Drinks
- Fitness
- Gardening
- Dance
- Causes
- Film
- Crafts
- Other/General
- Cricket
- Grooming
- Technology